Innovatoren-Porträt: Rohstoff-Handling Mit dem Gespür für Rohstoffe – intelligente Rohstoffautomatisierung und -logistik vom Experten
Die Dosierung, der Transport oder die Verarbeitung von Schüttgütern ist seit Jahrhunderten fast immer eine mechanisch verfahrenstechnische Aufgabe. Es sei denn, AZO hat die Finger im Spiel. Der Spezialist für die intelligente Rohstoffautomation aus dem Neckar-Odenwald-Kreis schafft es, ehemals rein mechanisch verfahrenstechnische Prozesse ins Industrie 4.0-Zeitalter zu heben.
Je komplizierter das Handling eines Rohstoffes, etwa weil dieser schlecht fließt, klebt oder toxisch ist, desto wohler fühlt sich AZO. Gerade, wenn’s schwierig wird, sieht sich der Osterburkener Rohstoffexperte an seiner Ehre gepackt – und sorgt dafür, dass alle Rohstoffe in der richtigen Menge und zum richtigen Zeitpunkt an Ort und Stelle gelangen.
Wie dies gelingt? Als erstes ist das Detailwissen rund um Rohstoffe zu nennen. Im bestens ausgestatteten Schüttgutlabor werden seit Jahrzehnten die unterschiedlichsten Rohstoffe analysiert und in einer Datenbank erfasst. Dabei werden Partikelgrößenverteilung und Partikelform charakterisiert, die Schütt-, Stampf- und Feststoff-Dichte bestimmt, sowie Fließeigenschaften im unbelüfteten und belüfteten Zustand analysiert. Schließlich kann sich selbst ein scheinbar gleicher Rohstoff an unterschiedlichen Produktionsstandorten unter anderen Gegebenheiten (Stichworte sind hier Luftdruck, Luftfeuchtigkeit oder Temperaturschwankungen) völlig anders verhalten.
Mindestens genauso wichtig sind jedoch die Neugierde und Offenheit für visionäre Technologien sowie der unbedingte Einsatz von Automatisierung und Digitalisierung möglichst vieler Prozessschritte in den Systemen, immer fokussiert auf die Bedürfnisse der Kunden. Die über 1.000 Mitarbeiter liefern somit nicht nur einzelne Systeme, sondern suchen immer wieder nach neuen Ideen, wie sich die Rohstoffautomation wirtschaftlich und zukunftssicher gestalten lässt. Insbesondere in der intelligenten Rohstoff-Automation und -Logistik hat sich AZO in den vergangenen Jahrzehnten einen Namen gemacht.
Dabei deckt das Portfolio alle Branchen von Food, Pharma über Kosmetik bis hin zu Chemie und Kunststoff ab. Ähnlich breit ist das Angebot bei den Komponenten und Systemen. Von den verschiedenen Standorten aus werden Einzelkomponenten für das Lagern, Austragen, Sieben, Fördern, Dosieren, Wiegen und Automatisieren von Rohstoffen – wie pneumatische Fördersysteme, Siebmaschinen und Schüttgutcontainer – über innovative Systeme zum Dispergieren, Mischen und Homogenisieren von flüssigen und halbfesten Produkten bis hin zur Turn-Key-Lösung weltweit geliefert.
Jede Branche stellt spezifische Anforderungen
Sich auf bewährten Technologien auszuruhen, ist jedoch nicht der Anspruch von AZO. So ergeben sich täglich neue Herausforderungen durch neue Märkte, seien es vegane Nahrungsmittel, ein steigendes Interesse an Recycling-Lösungen, oder die Elektromobilität. „Das staubfreie Handling von Rohstoffen für Batteriemassen ist extrem herausfordernd“, nennt CTO Klaus Kilian ein Beispiel. Hier müssen nicht nur der Produktschutz, sondern eben auch die Sicherheit des Bedieners bedacht werden. Hinzu kommen die speziellen Eigenschaften des Rohstoffes, der sehr hohe Anforderungen stellt.
Auch das Pulverhandling für 3D-Druck, die additive Fertigung sorgt für ganz neue Aufgaben. „Üblicherweise sind unsere Systeme Unikate, aber für diese Branche liefern wir auch baugleiche Anlagen“, so Kilian. Im Gegensatz zu anderen Anlagen des Unternehmens müssen die Systeme für das Pulverhandling im 3D-Druck auf engstem Bauraum installiert werden. Während bei anderen Branchen ein Scale-up nach vorgegebenen Regeln folgt, ist das in dieser Branche notwendige Scale-down aufgrund der erforderlichen Systemgrößen ausgesprochen komplex. „Manche Dinge funktionieren einfach nicht mehr, wenn die Systeme kleiner werden. Dies gilt vor allem bei den schlecht fließenden, feinkörnigen Metallpulvern“, erklärt Kilian.
Mittlerweile gelten die Osterburkener als Experten für die automatische Beschickung von 3D-Druckern zur additiven Fertigung und zwar sowohl für Metallpulver als auch Kunststoffpulver, das Lagern, Bereitstellen, Konditionieren, Transportieren und Aufbereiten der verschiedensten Pulver. Diese Expertise schätzt die Branche, so ist AZO seit mehreren Jahren Kooperationspartner für den französischen Metall-3D-Druck-Spezialisten AddUp.
Von der Cloudlösung bis zur Virtual Reality

„Die Datenanalytik wird eine immer größere Rolle spielen, um noch gezielter und schneller zu reagieren.“ Dieter Huspenina, Chief Sales Officer, AZO
(Bild: AZO)
„Die Datenanalytik wird in Zukunft eine immer größere Rolle spielen“, ist CSO Dieter Huspenina überzeugt. „Wir werden in Zukunft auf ganz unterschiedlichen Ebenen Daten erfassen und analysieren, damit wir noch gezielter und schneller reagieren können.“ Dabei beschäftigt man sich mit neuen Aspekten der Datensicherheit, etwa in puncto Schutz der Automatisierungssysteme, wie Huspenina aufzeigt: „Wir haben uns unter anderem entschlossen, die Vorgaben der IEC 62443, Stichwort Security im OT Bereich, neben der bereits in der Implementierung befindlichen DIN EN 27001 schon jetzt anzugehen, obwohl dies für uns als Anlagenbauer noch nicht verpflichtend ist. Die Sicherheit unserer Kunden ist uns ein großes Anliegen.“
Mit Technologiesprüngen zum Leuchturm werden
„Wir waren schon vor der Pandemie in vielen Prozessen digital unterwegs, zum Beispiel mit digitalen Werker-Cockpits in der Fertigung, aber es sind weitere Anstrengungen nötig“, ist Kilian überzeugt. „Früher waren die Facharbeiter bei Start der Montage und Inbetriebnahme einmal ein halbes Jahr im Ausland auf der Baustelle“, schiebt Huspenina zur Erklärung hinterher. „Die Zeiten sind vorbei. Daher müssen wir uns überlegen, wie wir die Anlage so aufbauen, dass bei der Montage keine Fehler passieren.“ Dies gelingt unter anderem mit modularen Komponenten, so dass quasi ein Plug-and-Play im Anlagenbau möglich ist. „Die Systeme müssen aber auch in der Bedienung einfacher werden“, so die Erfahrung von Huspenina, gleiches gelte für die Wartung: „Das Ziel muss heißen, dass nicht mehr alle zwei Jahre eine Routinewartung stattfindet, sondern dass sich die Anlage von selbst meldet, wenn ein Bauteil auszufallen droht.“
Solche Konzepte müssen angesichts des Facharbeitermangels schnellstens umgesetzt werden, so Kilian: „Im Augenblick gibt es noch Anlagenführer mit 15- bis 20-jähriger Berufserfahrung, die kleinste Unstimmigkeiten an einer Anlage spüren oder hören.“ Obwohl man nicht alles durch Sensoren ersetzen kann, werden hier verstärkt digitale Werkzeuge zum Einsatz kommen.
Gemeinsame Projekte mit Forschungseinrichtungen, wie der TU Darmstadt, ZML in Heilbronn oder der RWTH Aachen weisen bereits Lösungen auf. Zu den Leuchtturmprojekten gehört etwa Prometheus. Hier wurde mithilfe der künstlichen Intelligenz eine selbstregulierende Förderung entwickelt. Dabei wird das momentane Verhalten der pneumatischen Saugförderung über Sensoren gemessen und über maschinelles Lernen an ein je nach Aufgabenstellung vorgegebenes Optimum herangeführt.
:quality(80)/images.vogel.de/vogelonline/bdb/1741800/1741898/original.jpg)
Robotik schützt Produkt und Bediener
Auch in der Intralogistik wurden mit dem RoLog-System neue Wege eingeschlagen. Der Roboter RoLog stellt Kleinkomponenten als Teilrezeptur zusammen, wobei Komponentengrößen von 50 g bis 5 kg möglich sind. Damit wird die aufwändige manuelle Wiegung von Kleinstmengen ersetzt. Eine Sicherheitszelle um den Roboter ermöglicht dabei absoluten Produkt- und Bedienerschutz. Dadurch können selbst hochkritische und gesundheitsschädliche Rohstoffe problemlos dosiert werden und dies bei einer Verfügbarkeit von 24/7.
Innovationsklima im gesamten Unternehmen fördern
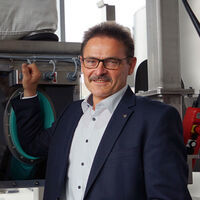
„Uns geht es darum, bei jedem Mitarbeiter die Innovationsbereitschaft fest zu verankern.“ Klaus Kilian, Chief Technology Officer, AZO
(Bild: AZO)
Das Ziel von AZO ist ein neues Mindsetting auf dem Weg zur digitalen Transformation. Rohstoffautomation beinhalte zwar immer noch viele mechanisch verfahrenstechnische Vorgänge, die jedoch mit intelligenten digitalen Werkzeugen kombiniert werden müssen, wovon wiederum unsere Kunden profitieren“, ist sich Huspenina sicher.
„Wir haben die virtuelle AZO-Welt aufgesetzt, führten Hackathons durch und suchen mit Start-ups nach neuen Lösungen.“ berichtet Kilian, der betont, dass dabei nicht immer nur das Ergebnis zählt: „Uns geht es vielmehr darum, ein Innovationsklima zu schaffen und bei jedem Mitarbeiter die Innovationsbereitschaft zu fördern und fest zu verankern. Ich bin davon überzeugt, dass sich dies in unseren Systemen und Komponenten widerspiegelt, damit auch weiterhin alle Rohstoffe in der richtigen Menge und zum richtigen Zeitpunkt an Ort und Stelle gelangen.“
(ID:47848325)
Dieser Beitrag Mit dem Gespür für Rohstoffe – intelligente Rohstoffautomatisierung… stammt aus folgender Quelle www.process.vogel.de und wurde am 2021-12-09 00:01:00 veröffentlicht.