Energieeffizienz
Wie behält die Schüttgut-Branche Energiekosten im Griff?
Anbieter zum Thema
Steigende Energiepreise, die CO2-Reduzierung, verbunden mit der Frage, wie sich eine nachhaltige Produktion gestalten lässt, zählen derzeit zu den großen Herausforderungen. Auch die Schüttgutbranche sucht nach Lösungen, wie sich diese Themen vor dem Hintergrund der Wirtschaftlichkeit darstellen lassen.
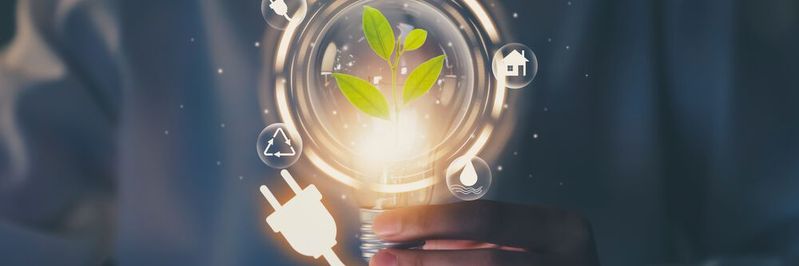
(Bild: © sitthiphong – stock.adobe.com)
Als im vergangenen Sommer die Energiekosten immens stiegen, zogen einige Unternehmen den Stecker und drosselten ihre Produktion. Zwar haben sich die Märkte etwas beruhigt, die Kosten sind jedoch immer noch hoch und werden auf absehbare Zeit wohl nicht merkbar sinken. Es lohnt sich also, weitere Stellhebel in Bewegung zu setzen. Nicht zu vergessen: auch viele Nebenprozesse, etwa Druckluftanlagen, Pumpen, Förderer oder Lüfter, bieten erhebliche Einsparpotenziale. Pumpen beispielsweise laufen häufig weit außerhalb ihres ursprünglich absehbaren Betriebspunktes und sind damit weit entfernt von einem optimalen Energieeinsatz. Erschwerend kommt hinzu, dass Pumpen oft aus einem vermeintlichen Sicherheitsgedanken heraus mit 10- bis 15-prozentigen Zuschlägen bestellt werden und sich schon von vorneherein nicht im Optimum befinden.
Auch die effiziente Steuerung von Prozessabläufen kann dazu beitragen, den Energieverbrauch zu reduzieren, zum Beispiel wenn es darum geht, unnötige Stillstandzeiten zu reduzieren oder Verbraucher, die sich im Stand-by-Modus befinden, gezielt abzuschalten.
Fokus auf die Optimierung thermischer Prozesse
Besonders hohe Potenziale zur Senkung von Energiekosten bietet die Optimierung thermischer Prozesse. So benötigt eine thermische Trocknung im Vergleich zu einer rein mechanischen Entwässerung bis zu zehnmal mehr Energie. Die Rückgewinnung von Abwärme kann den Energieverbrauch erheblich senken. Wie das funktioniert, zeigt Allgaier Process Technology, die von einer Energieeinsparung bis zu 30 Prozent bei thermischen Trocknungsprozessen ausgehen. „Durch das teilweise Kondensieren von feuchter Trocknerabluft in individuell ausgelegten Wärmetauschern kann zusätzlich die latente Wärme der Abluft genutzt werden, was die Effizienz weiter erhöht. Außerdem kann bei einem kombinierten Trocknungs- und Kühlprozess die Restwärme aus dem getrockneten Feststoff durch Rückführung der Abluft aus der Kühlzone rückgewonnen werden“, beschreibt Daniel Mössinger, Vertriebs- und Projektingenieur bei Allgaier Process Technology die Vorgehensweise. „Um den Einsatz fossiler Brennstoffe weiter zu reduzieren, besteht zudem die Möglichkeit, dass die rückgewonnene Wärme mit Wärmepumpen auf ein höheres Temperaturniveau gebracht wird. Dadurch kann diese noch effizienter zur Trocknerbeheizung verwendet werden.“ Weiter lohnt es sich, auch die vor- und nachgelagerten Prozessschritte im Auge zu behalten. Bei dem Design von Neuanlagen kann zusätzlich der Effekt der Verdunstungskühlung berücksichtigt werden. Neben der Wärmerückgewinnung empfiehlt Mössinger außerdem eine genaue Analyse des vorhandenen Trocknungsprozesses, um zum Beispiel die Effizienz durch Anpassung des Trocknerdesignpunktes zu steigern.
Energieeffiziente Regelungen von Anlagen
Auch Markus Schindler, Sales Director Deutschland bei Envea, sieht bei der Optimierung von Trocknungsprozessen besonders hohes Potenzial. Sein Unternehmen setzt dabei auf Sensorik. „Dafür wird in der Regel die Materialfeuchte vor und nach dem Trockner erfasst, so dass die Trocknung optimal auf den Zielfeuchtegehalt abgestimmt werden kann“, erklärt Schindler. „Dies kann z. B. durch die Änderung der Verweildauer des zu trocknenden Produkts im Trockner oder eine optimierte Regelung des Trockners selbst erreicht werden. Zum Envea-Portfolio gehören auch Sensoren zur Prozessoptimierung, erklärt Schindler: „Zum Beispiel können Absaugprozesse mit einer Volumenstrommessung möglichst energieeffizient geregelt werden.“ Ganz nach dem Motto: „So viel wie nötig, aber so wenig wie möglich.“ Mit den Flow-Produkten des Unternehmens lassen sich zudem Förderprozesse von Schüttgütern hinsichtlich der Fördermenge und -geschwindigkeit so optimieren, dass auch hier Einsparungen erzielt werden. „Dies gelingt etwa durch eine energieeffizientere Regelung der Anlagen oder der Vermeidung von Ausschuss durch eine materialschonende Förderung“, nennt Schindler weitere Beispiele.
Energieeffizienz beginnt bei der Messung von Energieströmen
Schon das kontinuierliche Überwachen aller Energieflüsse während der Produktion sorgt dafür, dass ein Anlagenfahrer eine Anlage im Optimum fahren kann und damit Einsparungen von rund zehn Prozent gegenüber dem Anlagenzustand in der Komfortzone möglich sind. „Energieeffizienz beginnt immer damit, genau zu wissen, wie viel Energie wann und wo eingesetzt werden muss“, bestätigt Ludger Henke, MTS Messtechnik. „Damit steht jeder Anlagenbetreiber zunächst vor der Aufgabe, Stoffströme zu erfassen, z. B. durch Waagen. Erst auf Basis dieser Daten kann neben anderen Parametern auch der Energieeinsatz optimiert werden. Henke nennt als Beispiel den Veredelungsprozess von Rohperlite, der eine gleichbleibende Beschickung des Blähofens benötigt. Hierzu werden seit Jahren Bandwaagen eingesetzt, die die geförderte Menge Rohperlite erfassen und entsprechend eines variablen Sollwertes in den Blähofen abgeben. Für Henke werden damit gleich zwei Fliegen mit einer Klappe erschlagen: Somit wird sowohl der Energieeinsatz für den Betrieb des Ofens optimiert als auch eine gleichbleibende Qualität des Endproduktes Perlite gewährleistet.
Für den Anwender ist der Aufwand im Übrigen gering. Bandwaagen können in vorhandene Förderbänder und Anlagen häufig auch nachträglich integriert werden, ohne aufwändige Umbauten. „Sie sind wartungsarm und liefern zuverlässige und langzeitstabile Messergebnisse. Damit stellen sie immer wieder eine wirtschaftlich interessante Lösung zur Erfassung und Regelung von Stoffströmen dar“, so Henke.
Überhaupt ist der Aufwand, eine entsprechende Sensorik einzubauen, meist nicht sehr groß, so auch die Erfahrung von Schindler. „Unsere Sensoren sind sehr einfach zu installieren und in Betrieb zu nehmen. Die Anbindung an das Prozessleitsystem erfolgt meist ganz einfach über ein Analogsignal oder Modbus, so dass z. B. eine Trocknersteuerung auf Basis der Messdaten umgesetzt werden kann.“ Die Amortisationszeit hängt dabei von vielen Faktoren ab, wie der Einbausituation an der Anlage, dem erzeugten Produkt, dessen Wert, dem Ausgangs- und Zielfeuchtegehalt, den aktuellen Energiepreisen und mehr. Aber es lohnt sich in vielen Fällen, so die Erfahrung von Schindler: „Eine Messung kann sich in manchen Fällen innerhalb weniger Tage amortisieren, in anderen Fällen kann es auch ein bis zwei Jahre dauern“.
Bildergalerie
Die einzelne Komponente verbraucht nicht viel, aber die Summe macht’s
Neben den Trocknungsprozessen ist der Blick auf den Transport von Schüttgütern lohnenswert. „Weltweit werden täglich unzählige Mengen davon durch Fördersysteme bewegt, meist rund um die Uhr“, erklärt Ralf Schrage, Geschäftsführer von Schrage Rohrkettensystem Conveying Systems. Dies erfordert nicht nur eine enorme Menge an Energie; vielen Unternehmen ist der Verbrauch einzelner Fördersysteme gar nicht bewusst. „Umso wichtiger ist hier die richtige Wahl der Maschine für den jeweiligen Einsatz“, bestätigt Schrage. Zwar verbrauchen einzelne Komponenten, wie Förderschnecken, wenig Energie, aber: „Beim Einsatz einer Vielzahl solcher Systeme summiert sich der Energiebedarf enorm!“
Schrage geht mit seinen Rohrkettenförderern aber noch einen Schritt weiter. „Rohrkettenförderer bewegen Schüttgüter sehr schonend! Darüber hinaus wird deutlich weniger Kraft benötigt, um ein Produkt an seinen Zielort zu transportieren“, so Schrage. Dies gelingt durch die bewusste Auswahl und Abstimmung von Komponenten der Fördersysteme. Bei der Auslegung für den Einsatzfall wird darauf geachtet, dass nicht nur lange Standzeiten erreicht, sondern vor allem Werkstoffpaarungen eingesetzt werden, die möglichst wenig Widerstand erzeugen. Gleichzeitig sind die Systeme staubdicht; wodurch teure und vor allem energieraubende Filteranlagen entfallen. Es gibt aber noch einen weiteren Grund für die Energieeffizienz, wie Schrage erklärt: „Dank der Möglichkeit, auch 2- bzw. 3-dimensionale Linienführungen zu realisieren, sind im Vergleich zu anderen Techniken deutlich weniger Förderaggregate notwendig.“ Schrage nennt ein Beispiel: „Während eine Förderschnecke immer nur ‚geradeaus‘ fördern kann, realisiert unser Rohrkettenförderer aus Friedeburg verschiedenste ‚Richtungswechsel‘ − mit nur einem Antrieb.“ Will man auf die Rohrkettenförderer umsteigen, sind Becherwerke, Trogkettenförderer oder Förderschnecken meist 1:1 in ihrer Linienführung ersetzbar. Anpassungen bestehender Anlagen sind allerdings nur bedingt möglich. „Natürlich können grundsätzlich energieeffiziente Antriebe mit alten Aggregaten getauscht werden. Jedoch lässt sich eine energieintensive Technik wie eine pneumatische Anlage meist nicht so weit umrüsten, dass man von einer energiesparsamen Fördertechnik sprechen kann, so Schrage, der dann für einen Technikwechsel plädiert. „Vergleichsweise verbrauchen unsere Rohrkettenförderer mitunter nur zehn Prozent der Energie von pneumatischen Anlagen. Tauscht man also eine Pneumatik gegen Rohrkettenförderer, spart man bis zu 90 Prozent der Energie. Nicht nur in diesem Beispiel entfällt dann zusätzlich die Trennung von Produkt & Luft – auch für weitere Fördersysteme.“
Effizienz-Label für Fördergurte
Doch auch für Förderbänder gibt es Möglichkeiten, den Verbrauch zu senken. So kennzeichnet Continental nun seine Produkte mit einem Energieeffizienz-Label, das das Unternehmen gemeinsam mit der US Association for Rubber Products Manufacturers (ARPM) entwickelt hat. Je nach Rollwiderstand der im Fördergurt verwendeten Mischung, reicht die Energieeffizienz von Klasse A (beste Energieeinsparung) bis hinunter zur Klasse G. Immerhin macht der Gurt bis zu 60 Prozent des Energieverbrauchs der gesamten Anlage aus. Der entscheidende Faktor für die Energieeffizienz von Fördergurten ist ihr Rollwiderstand. Zu diesem Zweck hat Continental für die unteren Deckplatten der Serie „Conti Eco“ energieoptimierte Gummimischungen entwickelt, die den Rollwiderstand auf der Fördergurtanlage minimieren. Je nach Anlagenkonzeption können mit dem Fördergurt „Eco Plus“ 15 Prozent und mit dem „Eco Extreme“ bis zu 30 Prozent Energie im Vergleich zu einem standardmäßigen Fördergurt eingespart werden. Oder anders ausgedrückt: bei einer Förderanlage mit einer Länge von fünf Kilometern kann die Eco Extreme-Lösung mehr als 1.500.000 kWh pro Jahr einsparen.
(ID:49535124)
Dieser Beitrag Wie sich nachhaltige Produktion gestalten lässt stammt aus folgender Quelle www.process.vogel.de und wurde am 2023-07-04 13:06:18 veröffentlicht.
Originalbeitrag