Direktverpressung Ist die Direktverpressung der Königsweg in die Kontiproduktion?
Die Vorteile des Continuous Manufacturing bei der Herstellung oraler fester Arzneiformen sind mittlerweile unumstritten. Wie die Direktverpressung den Weg in die Kontiproduktion ebnet, zeigt eine Lösung von Fette Compacting.
Firmen zum Thema
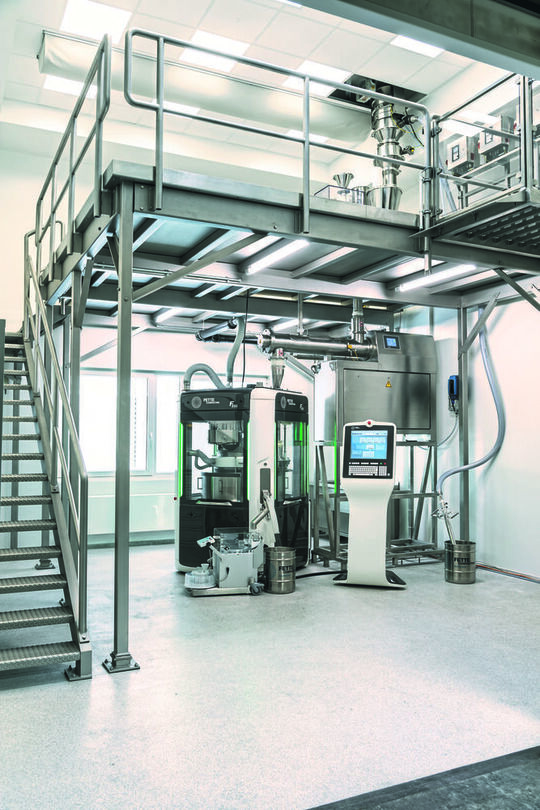
Steigender Druck in Bezug auf kürzere Markteinführungszeiten, verbesserte Produktqualitäten, geringere Kosten und flexiblere Produktionsmethoden – dies sind die wichtigsten Gründe, warum Pharmahersteller neben ihren klassischen Batch-Anlagen vermehrt auf kontinuierliche Produktionslinien setzen. Auch unterstützen Regulierungsbehörden wie die Food and Drug Administration (FDA) diesen Produktionsansatz. In der Folge werden immer mehr orale feste Arzneiformen (Oral Solid Dosage, OSD) mittels Continuous Manufacturing produziert. Erste Erfahrungen der Hersteller bestätigen die Einsparungen, die durch das Kontiverfahren möglich sind.
Etablierte Presse auf kontinuierlichen Wegen
Auch bei Fette Compacting, Schwarzenbek, setzt man auf die kontinuierliche Produktion in der Tablettenherstellung. Auf das Direktverpressungssystem angesprochen, hebt Dr. Marten Klukkert, Manager Technology Center bei Fette Compacting, direkt die Vorteile der Tablettierlösung hervor.
So sei die Kernkomponente der Linie die Tablettenpresse FE 55 keineswegs neu, sondern seit über zehn Jahren auf dem Markt und bei vielen Top-Playern der Pharmaindustrie erfolgreich im Einsatz. „Die FE55 haben wir wegen ihrer besonderen Produktionsflexibilität und besonderen Eignung zur Direktverpressung von Pulverformulierungen gewählt und für den kontinuierlichen Gesamtprozess optimiert.“
Wer nun auf die kontinuierliche Produktion setzen möchte, kann die bestehende Anlage ohne aufwändigen Umbau umrüsten und umvalidieren. Dafür halten sich zusätzliche Investitionen in Grenzen.
Auch im täglichen Betrieb gibt es für die Bediener wenig Neuerungen, wie Klukkert erklärt: „Die Steuerung und die Bedienoberfläche sind angelehnt an die FE 55, lediglich die Aspekte der kontinuierlichen Fertigung werden ergänzt, etwa in Form von zusätzlichen Prozessparametern und Meldungen einiger Sensoren.“
Time-to-market lässt sich verkürzen
Prinzipiell sieht Klukkert drei entscheidende Vorteile beim Kontiverfahren: Höhere Produktionseffizienz, größere Produktqualität und verkürzte Time-to-market, wobei der letztgenannte Aspekt in Zukunft der entscheidende sein wird. „Üblicherweise benötigt man mehrere Wochen bis Monate, um einen neuen Produktionsprozess aufzusetzen und zu validieren. Nun ist eine viel schnellere Prozessentwicklung möglich und auch das Scale-up gelingt schneller“, erklärt Klukkert, der auf die Erfahrungen aus dem Markt verweist. „Jede Woche, die man hier spart und früher auf den Markt kommt, lohnt sich enorm“, so Klukkert. Damit erweitern Pharmaunternehmen die Zeitspanne, um die Entwicklungskosten eines Medikamentes wieder herein zu bekommen.
Effizientere Produktion ist nun möglich
Im Vergleich zur Produktion im Batch-Betrieb sind kontinuierliche Anlagen deutlich platzsparender und kostengünstiger. Schließlich wird das Pulver nach der Dosierung direkt vom Mischer in die Tablettenpresse geleitet. „Der durchgängige Materialstrom erfordert keinen Lagerraum für Zwischenprodukte und ermöglicht es, Losgrößen allein über die Laufzeit der Anlagen zu skalieren. Dadurch werden teure Reinraumflächen frei“, nennt Klukkert einen weiteren Vorteil.
Neues Prozessverständnis ist nötig
Allerdings erfordere dies ein verändertes und neues Prozessverständnis, so Klukkert. Viele vormals getrennte Prozesse und Komponenten wachsen zu einer Linie zusammen. Um nur ein Beispiel zu nennen: Versuchsläufe und die spätere Produktion finden auf der gleichen Anlage statt. Der Materialverbrauch zur Prozessentwicklung wird so deutlich reduziert.
:quality(80)/images.vogel.de/vogelonline/bdb/1802600/1802676/original.jpg)
Grundsätzlich gilt dabei: Je schlanker das Design der Gesamtanlage, desto größer die Kontrolle und die Effizienz des Produktionsprozesses. „Man muss die Balance zwischen hoher Qualität und niedriger Komplexität halten, um mit der kontinuierlichen Produktion Erfolg zu haben“, ist Klukkert überzeugt.
Höhere Produktqualität dank besserer Prozesssteuerung
Das Herzstück der neuen Direktverpressungslinien bilden die Tablettenpressen der FE-Serie. Diese bilden zusammen mit einem horizontalen Mischsystem und hochpräzisen Dosierern eine sichere und effiziente kontinuierliche Anlage für einen breiten Kapazitätsbereich. „Nun ist ein homogener Fluss möglich, bei dem jeder Schritt engmaschig überwacht werden kann“, so Klukkert.
Außerdem lassen sich relevante Parameter synchron einstellen und man kann auf Abweichungen dynamisch reagieren. Aufgrund der geringen Hold-up Masse in der Direktverpressungslinie ist eine bessere Prozesssteuerung und schnelleres Erreichen eines stabilen Produktionszustandes möglich. „Es gibt weitere positive Nebeneffekte, zum Beispiel führen Vibrationen beim Transport von Zwischenprodukten schon einmal zu einer Entmischung, sodass diese vor ihrem Einsatz noch einmal gemischt werden müssen. Bei der Direktverpressung ist eine solche Entmischung eigentlich nicht möglich.“
Qualitätsparameter kontinuierlich erfassen
Die hohe Effizienz und Produktqualität einer kontinuierlichen Produktionslinie wird durch den Einsatz von Echtzeit-Qualitätskontrollsystemen sichergestellt. Mittels PAT-Systemen werden hierzu die kritischen Material- und Qualitätsattribute des konstanten Materialstroms laufend erfasst. Zwar lassen sich bisher nicht alle Parameter in Echtzeit freigeben, aber für das Prozessmonitoring spielt PAT eine große Rolle. Für die Echtzeitanalyse setzt Fette Compacting primär auf die Nahinfrarotspektroskopie (NIR).
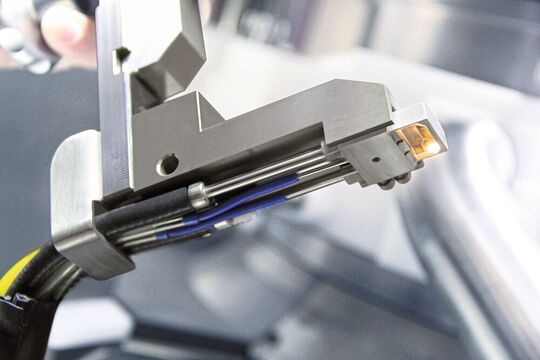
NIRS-Messkopf für die Tablettenpresse im Inline-Modus.(Bild: Fette Compacting)
Ein NIR-Sensor in der Tablettenpresse erlaubt es, jede einzelne Tablette auf die enthaltene Wirkstoffkonzentration zu untersuchen und den Produktionsprozess anhand der gewonnenen Daten zu optimieren. „Wenn NIR-Sensoren an ihre Leistungsgrenze stoßen, beispielsweise bei niedrigen Wirkstoffkonzentrationen oder bei NIR-inaktiven Wirkstoffen, setzen wir auf die Raman-Spektroskopie“, ergänzt Klukkert.
Direktverpressung in der Testanlage prüfen
Ausblick: Interessant ist die Direktverpressung sowohl für kleinvolumige als auch für große Chargen. Beim Einstieg in das Kontiverfahren unterstützen die Prozess- Experten aus Schwarzenbek, indem sie die Verarbeitbarkeit einer konkreten Formulierung überprüfen und die Entwicklungsphase der kontinuierlichen Linie begleiten.
Im Competence Center in Schwarzenbek steht eine Testanlage für die Direktverpressung bereit. Die Produktionslinie enthält eine Tablettenpresse der FE-Serie, ein Mischsystem und bis zu sieben Dosierer. „Es geht uns darum, dass der Gesamtprozess handelbar bleibt und nicht in Komplexität ausufert“, gibt Klukkert die Zielrichtung bei der Kontifertigung vor.
(ID:47808273)
Dieser Beitrag Ist die Direktverpressung der Königsweg in die Kontiproduktion? stammt aus folgender Quelle www.process.vogel.de und wurde am 2021-12-08 17:24:00 veröffentlicht.